Glue Glossary: Defining Roofing Adhesive Terms
Published: 20 February 2024
Updated: 20 February 2024
There are many terms within the roofing adhesive industry which can be difficult to understand. Here we define some common terms you may come across.
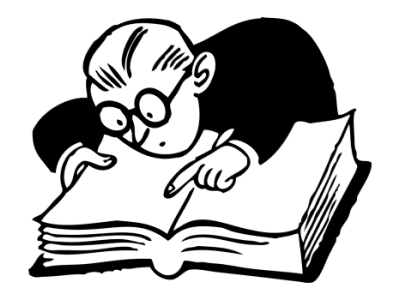
Adhesive:
An adhesive is a product that is used to bond surfaces or objectives together. Roofing adhesives will bond insulation and membranes to surfaces.
Ambient temperature:
Ambient temperature refers to the temperature around the objects being bonded.
AVCL:
Air Vapour Control Layers (AVCLs) are designed to reduce water vapour accumulating within a building structure. An AVCL is typically installed before insulation layers to control the passage of warm air.
BUR:
Built-Up Roofing (BUR) is a flat waterproofing method that combines several layers of material built on top of each other, including layers of bitumen or asphalt.
Coat Weight:
Coat weight is the amount of adhesive required per square metre to give the required performance.
Consolidation:
Consolidation refers to the process of applying pressure to area that has been bonded. For contact adhesives, it is important that the bond is consolidated correctly using a roller to ensure the layers of adhesive fuse together to form a homogenous layer.
Coverage Rate:
Coverage rate is the area that a container of adhesive will cover to provide the correct coat weight to give the required performance.
Curing:
Curing refers to a chemical reaction that occurs during the application or use of the adhesive. It is the result of two-components reacting or cross-linking, resulting in a physical change from a liquid to a solid. This process is irreversible.
Cure-Time:
Cure-time is the amount of time for the chemical reaction to take place and for the adhesive to harden and reach full strength.
Detail Areas:
Detail areas of a roof include the upstands, roof edges and junctions. Securing to detail areas is often the most difficult part of a roofing membrane installation as it involves bonding to vertical surfaces, often around apertures.
Diisocyanates:
Diisocyanates are a family of chemical building blocks mainly used to create polyurethanes. These chemical building blocks are reacted with polyols to form a polyurethane e.g. polyurethane foam or moisture-curing polyurethane adhesives and two-component polyurethane adhesives.
Drying:
Drying refers to the loss of liquid components of the adhesive. It is the evaporation of the carrier (the water or solvent added to make the adhesive liquid), which results in a solid film.
Drying-time:
Drying-time is the time taken for the carrier to evaporate and the product to harden.
EPDM Membrane:
Ethylene Propylene Diene Monomer (EPDM) membranes are black elastic synthetic rubber single-ply membranes that are cost effective and exhibit excellent weathering properties.
Fleece-Backed Membrane:
Fleece-backed membranes have a layer of material on the underneath of the membrane, which can add thickness and strength.
Fully-adhered:
Fully adhered roofing systems attach the membrane to the roofing assembly through the use of adhesives, without piercing the membrane. This method secures the membrane across the entire roofing assembly.
Hot-Melt Waterproofing:
Hot-melt waterproofing, also known as structural waterproofing, is a hot applied polymer modified bitumen solution, typically applied in 2 layers with a reinforcement layer. It is traditionally used within inverted/buried roof build ups.
Insulation:
Flat roofing insulation forms one element of a roofing system. It is of the main ways to reduce heat loss from properties and increase the building’s energy efficiency. There are a variety of insulation types available on the market, including EPS, XPS, PIR boards (including tissue and foil-faced), mineral wool and Foamglas.
Liquid-Applied Membrane:
Liquid-applied membranes are cold-applied roofing systems that cure to form a completely seamless and joint-free waterproof coating. They provide a hard-wearing and long-lasting waterproofing solution, even around complex details. Applied by brush or roller, they can conform to any shape.
Moisture-Curing:
Moisture-curing adhesives react with moisture in the air/substrates to cure.
Non-Backed Membrane:
Non-backed membranes are roofing membranes that tend to fall into three main polymer types (EPDM, TPO and PVC). All three types have specific properties that will affect how they can be adhered. Unlike fleece-backed membranes, they do not have the fleece layer.
One-Component:
One-Component adhesives are made of one-part. They include adhesives such as moisture-curing and contact adhesives.
One-Way Stick:
One-way stick adhesives are applied to one surface. They are generally solvent-free products, such as moisture-curing polyurethane or two-part polyurethane adhesives. These types of adhesives are curing products, which turn from a liquid to a solid via their curing mechanism.
Open-Time:
Open-time is the maximum amount of time available after an adhesive is applied to bond the substrates together before the adhesive solidifies.
Polyurethane:
Polyurethanes are created by reacting diisocyanates with polyols. Polyurethane adhesives are versatile, flexible and durable, capable of withstanding extreme conditions and temperatures.
Porous Substrate:
A substrate that allows water/air to pass through it.
Primer:
Primers are designed to help prepare roof surfaces before bonding. They help to seal the surface and improve the adhesion of the adhesive or coating being applied. Primers come in a variety of different forms and are often substrate specific. The type needed will depend on the substrate and the type of coating being applied.
PVC Membrane:
Polyvinyl Chloride (PVC) membranes are flexible and durable single-ply membranes, available in a range of colours.
RBM:
Reinforced Bituminous Membrane – RBM is one of the most used forms of flat roof waterproofing due to its durability. Common application methods include ‘pour and roll’ and torch-on. With the fire risk associated with these methods, our BUR & RBM range consists of high-performance polyurethane adhesives, developed specifically for flame-free installations.
Self-Adhesive Membrane:
Self-adhesive roofing membranes are waterproofing membranes with a peel-and-stick application.
Shelf-Life:
The shelf-life of an adhesive is the length of time from the date of manufacture for which it remains fit for use and will still behave according to the technical data sheet. It is the time it can be stored without any changes to its properties.
Single-Ply Membranes:
Single-ply membranes are strong, flexible sheets predominantly formed of synthetic polymers. They are sealed at the seams to form a continuous waterproofing layer. Combined with an insulation layer, they provide durable and efficient roofing systems.
Solids Content:
Solids content refers to the amount of base product left of an adhesive after the solvent/carrier has evaporated. It is expressed as a percentage.
Substrate:
Substrate refers to the surface that the product is applied to. Substrates must be clean, dry and free from frost and contamination. Different substrates will present different problems; however, primers can be used to seal a surface and help adhesion.
Tack:
Tack is known as the initial stickiness of the adhesive. High-tack adhesives form a bond of high strength immediately after the adhesive and surface are brought into contact.
Tack-Time:
Tack-time indicates the period of time that a bond can formed when the adhesive is brought into contact with a surface.
TPO Membrane:
Thermoplastic Polyolefin (TPO) membranes are durable single-ply roofing membranes that, unlike PVC membranes, contain no plasticisers.
Two-Component:
Two-component adhesives have two parts – it is the reaction of the individual parts mixing that causes the curing process.
Two-Way Stick:
Two-way stick adhesives are otherwise known as contact adhesives. These adhesives are generally solvent based. The adhesive is applied to both surfaces that are being bonded (for example, the substrate and membrane). Time is then allowed for the adhesive to dry or solvent to evaporate before the coated surfaces are put together.
Viscosity:
Viscosity is an adhesive’s ability to resist flow. In warmer temperatures, viscosity can decrease, with the product becoming thinner than usual. In colder temperatures, the viscosity can increase, with the adhesive becoming thicker than expected. Both scenarios can impact the application and expected coverage of the product.
Water-Based:
Water-based adhesives are created by combining water and polymers. The adhesive bond is made as the water evaporates or is absorbed by the substrate. Water-based adhesives are ideal for flat roofing projects where odour, solvent use and flammability is an issue, including occupied buildings and residential buildings.
Wind Uplift:
Wind uplift occurs when wind comes into contact with buildings. When the force of the wind hits the side of the building, it is pushed upwards, and the pressure is accelerated. When it reaches the top of the building it can return to its normal course, however it leaves reduced or negative pressure behind before settling back down over the roof. The combination of positive pressure and the negative pressure above the roofing surface results in a push-pull effect. In strong winds, the positive pressure under a roof can become greater than the negative pressure above it, which can separate the roofing materials and cause the structure to lift.
Wind Uplift Test:
A dynamic wind uplift test is a simulated full-scale test which is carried out on a specimen replicating a whole assembled roofing system, including the load bearing structure, adhesives, insulation and membrane. It is designed to replicate how a roofing system is installed in practice. Each specimen is then placed in a sealed pressure chamber and a computer-controlled valve system is used to stimulate ‘real’ wind suction pressure. The testing determines the dynamic uplift resistance (DUR) of a roofing system. The result provides data to estimate the structural resistance of a roofing system and ensures it meets wind load design requirements. The calculated wind uplift loads on the system must be proven to be less than the maximum design resistance of the system proposed.
Sign up to our newsletter to get our blogs delivered straight to your inbox
This form is protected by reCAPTCHA and the Google Privacy Policy and Terms of Service apply.