PU Liquid-Applied Membranes – Application Advice for a Durable Waterproofing Solution
Published: 05 September 2023
Updated: 05 September 2023
LAMs can be a durable flat roof waterproofing choice, provided they are applied correctly - here we offer our advice.
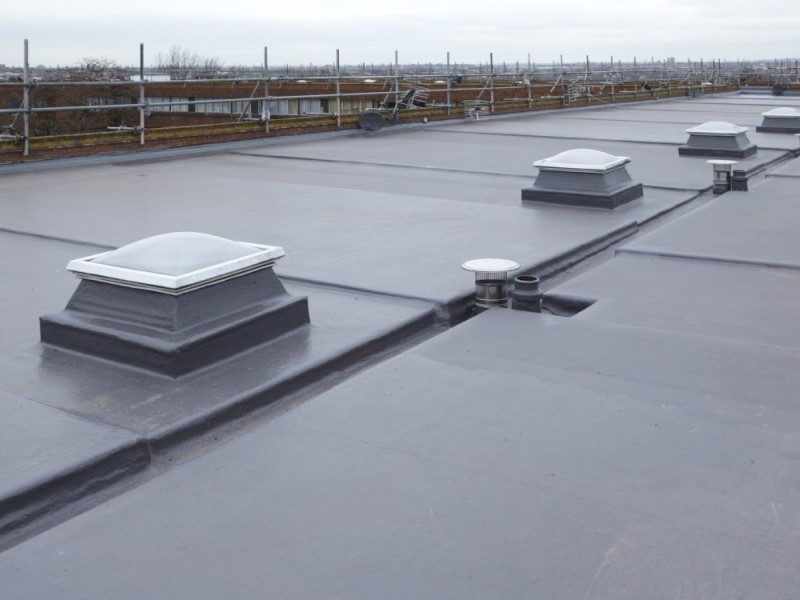
Liquid-applied membranes (LAMs) are becoming an increasingly popular choice for flat roofing projects due to their durability, versatility, and reliability.
Polyurethane (PU) liquid-applied membranes are generally cold-applied, single-component roofing systems that cure to form a completely seamless and joint-free waterproof coating. Systems are largely multi-layer, consisting of a basecoat, an embedded glass-fibre mat layer to reinforce the coating, and one or more topcoat layers. Once cured, it forms a tough, flexible coating that is weatherproof and tolerant to extreme temperatures, water, and chemicals. The ease of application make LAMs particularly suited to roofs with multiple upstands and complex detailing.
Durable Roofing Solution
Suitable for overlay, LAM systems are ideal for refurbishment projects, helping to extend the life of the roof, without the cost of replacement. Offering durability and longevity, systems can have a lifespan of 25+ years (depending on number of coats). LAM systems are usually compatible with a wide range of roof substrates – there is no requirement of ripping up the existing waterproofing, reducing landfill. Therefore, LAMs can be a sustainable flat roof waterproofing choice, provided they are applied correctly.
Application Advice
Storage
Products should be stored between 5-25°C in a cool, well-ventilated and covered area. Do not leave the products outside exposed to the elements or in direct sunlight. Keep only the materials that are planned to be used on that day on the roof.
Surface Preparation
Ensure surfaces are clean, dry, and free from debris and any other contaminants. Repair cracks, holes, and other defects prior to waterproofing application to ensure a smooth and sound substrate.
Most substrates require priming prior to application of the basecoat. It is recommended that peel-strength adhesion tests are carried out onsite to check compatibility with the substrate and to determine priming requirements before full-scale application. LAM primers have been formulated for specific applications/substrates – installing an incorrect primer could lead to system failure in the future.
Application
Always read the manufacturer’s product data sheet thoroughly before commencing work.
Apply to details prior to waterproofing horizontal surfaces.
Always apply the specified coat weight evenly and ensure the correct working time is followed. This will allow for full bonding of the membrane to the substrate. Applying too much or too little could result in insufficient strength.
Only apply when the outside temperature is between 5-30°C.
In warmer temperatures, the product’s viscosity can decrease, with the product becoming thinner than usual. The thinner product can be more difficult to apply as it may spread too quickly, impacting the application and expected coverage. Do not apply the LAM when the outside temperature is above 30°C, or the desired coverage rates may not be achieved.
Both temperature and relative humidity will affect the cure rate of the coating. As a general rule, every 10°C increase in temperature reduces the reaction time by 50%. Adjust working times accordingly.
Roll the glass-fibre mat into the basecoat whilst it is still wet, ensuring that there are no creases and that the glass-fibre mat is fully coated. Overlap the glass-fibre mat a minimum of 50mm on itself to ensure consistent reinforcement of the coating.
Ensure the basecoat is fully cured before adding further layers. It is best practice to allow the layer to cure overnight and to apply the second layer the following day.
The amount and number of coats of the topcoat required will depend on the lifetime specification.
Conduct a thorough inspection during and after application to identify any pinholes or voids. Address these areas promptly with additional application to ensure a continuous and seamless membrane.
Following this best practice advice will ensure your result is a durable and long-lasting finished waterproof coating.
Our infographic below summarises our key advice:
You may also be interested in
Sign up to our newsletter to get our blogs delivered straight to your inbox
This form is protected by reCAPTCHA and the Google Privacy Policy and Terms of Service apply.